机床主轴制动控制方式的改进设计
发布时间:2018-07-10 22:34:02 点击率:
通常机床主轴电动机制动时,采用的是能耗制动方式,使电动机AB相输入直流电源。
采用能耗制动方式使主轴电动机停止,主轴在低档位低速旋转时,大约需要0.5s,在高档位高速旋转时,大约需要2.5s。目前,采用的主轴电动机制动方法,先断开KM1,再闭合开关KM2,从而断开三相交流电源,接通直流电源,延时2.5s,认定主轴电动机停止旋转,然后进行换刀或其它动作。
主轴以不同的速度旋转时,采用能耗制动方式使主轴停止的所需时间不同,采用同样的能耗制动时间,延长无意义的加工辅助时间,降低了机床工作效率。另外,一旦开关KM2不能可靠闭合,或者直流电源保险断开不能正常提供直流电,则主轴电动机只能在摩擦力的作用下减速,制动时间需要很长,但延时2.5s后,机床数控系统仍然认定主轴电动机已经停止旋转,此时机床进行换刀或其它动作容易造成事故。
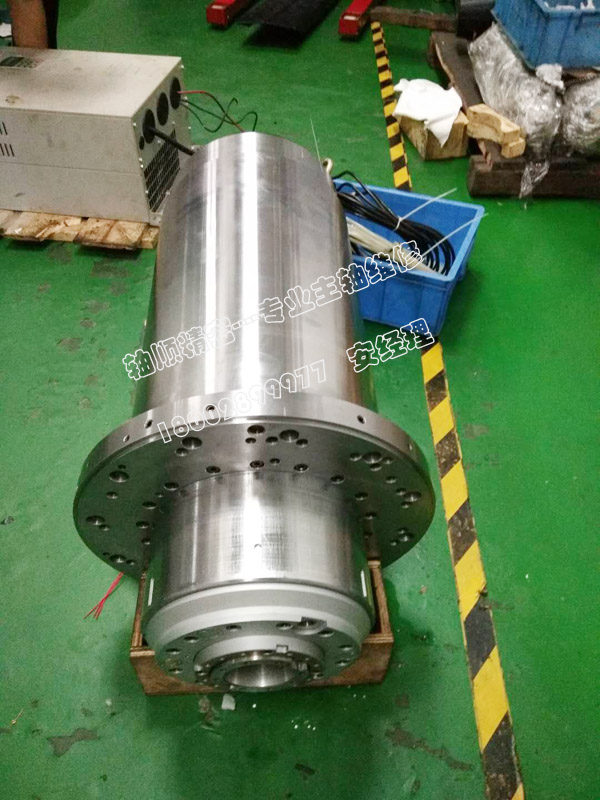
因此,我们对机床主轴制动控制方式进行了改进设计,判断主轴旋转状态,不采用延时2.5s,即认定主轴电动机停止旋转的控制方式,而是实时监控主轴旋转状态,当主轴旋转低于一定转速时,立即发出主轴停止完了信号。
主轴转速监测方案
在电动机的同步传动轴上安装一块条形铁片,和电动机同步旋转,由接近开关对其检测,每转检测到两个脉冲信号,通过对脉冲信号的检测而得知其转速。检测脉冲信号有两种方案。
第一方案:在一定周期Tp内读取脉冲信号的个数N,PLC是一种顺序控制器,它的程序是由前到后一步一步执行,每执行完一遍为一个扫描周期,然后从头开始循环执行。假如程序有2000步,每步执行时间周期为30μs,则程序的扫描周期约60ms,扫描频率约16Hz,能够准确检测出的脉冲频率应低于8Hz,当转速的脉冲频率大于16Hz,即转速n≥480r/min时,PLC受其扫描频率的影响,不能准确检测出脉冲的个数,情况不好时,会出现高速时检测的脉冲个数很少,误判为电动机基本停止而进行下面动作,造成事故。此种方案只适用于主轴低速旋转状态的监测。
第二种方案:检测脉冲信号持续为“0”或“1”的时间T,当n<60r/min时,发出主轴停止完了信号。由于PLC程序执行过程的延时,数控系统收到主轴停止信号,并执行下面动作时,主轴已完全停止旋转,n=60r/min所对应脉冲信号持续为“0”或“1”的时间T为0.25s,因此我们把检测脉冲信号的计时器设定为0.25s。同样高速时也会出现脉冲测不准的情况,但不管情况多坏,在0.25s的时间内“0”或“1”至少变化一次,因此可以准确地判断主轴是否停止旋转。此方案可以适用于主轴高速或低速旋转时主轴制动状态的检测。在实际应用中,我们采用了此方案。
PLC实现主轴能耗制动的控制方法
PLC设计程序中,X20.0为转速脉冲信号的输入,M05为主轴停止信号,Y50.0为主轴停止完了信号。
两个计时器TM1、TM2分别判断X20.0脉冲信号持续为“0”或“1”的时间是否达到设定的时间,只要有一个时间到达,即R100.1或R100.2变“1”,导致R100.3变“1”,此时M05为“1”,导致Y50.0输出“1”,则发出主轴制动完了信号,实现了主轴停止的准确判断。
采用能耗制动方式使主轴电动机停止,主轴在低档位低速旋转时,大约需要0.5s,在高档位高速旋转时,大约需要2.5s。目前,采用的主轴电动机制动方法,先断开KM1,再闭合开关KM2,从而断开三相交流电源,接通直流电源,延时2.5s,认定主轴电动机停止旋转,然后进行换刀或其它动作。
主轴以不同的速度旋转时,采用能耗制动方式使主轴停止的所需时间不同,采用同样的能耗制动时间,延长无意义的加工辅助时间,降低了机床工作效率。另外,一旦开关KM2不能可靠闭合,或者直流电源保险断开不能正常提供直流电,则主轴电动机只能在摩擦力的作用下减速,制动时间需要很长,但延时2.5s后,机床数控系统仍然认定主轴电动机已经停止旋转,此时机床进行换刀或其它动作容易造成事故。
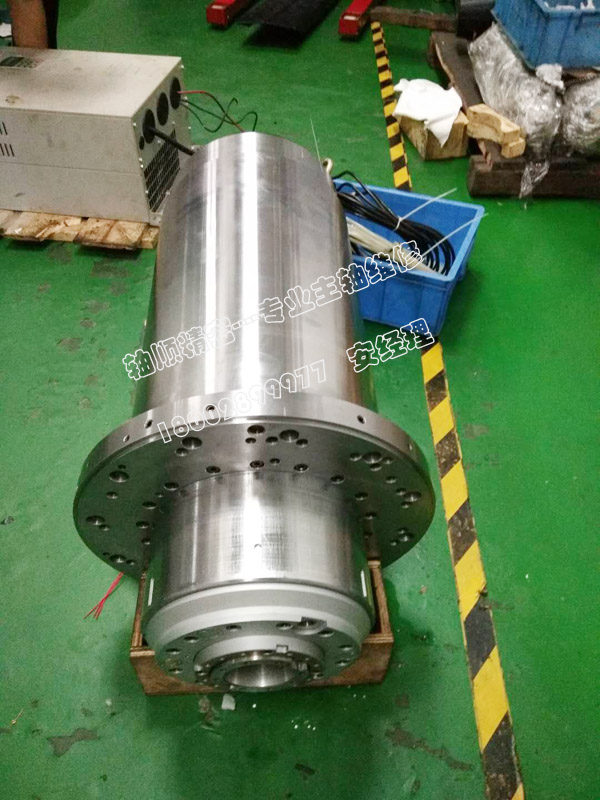
因此,我们对机床主轴制动控制方式进行了改进设计,判断主轴旋转状态,不采用延时2.5s,即认定主轴电动机停止旋转的控制方式,而是实时监控主轴旋转状态,当主轴旋转低于一定转速时,立即发出主轴停止完了信号。
主轴转速监测方案
在电动机的同步传动轴上安装一块条形铁片,和电动机同步旋转,由接近开关对其检测,每转检测到两个脉冲信号,通过对脉冲信号的检测而得知其转速。检测脉冲信号有两种方案。
第一方案:在一定周期Tp内读取脉冲信号的个数N,PLC是一种顺序控制器,它的程序是由前到后一步一步执行,每执行完一遍为一个扫描周期,然后从头开始循环执行。假如程序有2000步,每步执行时间周期为30μs,则程序的扫描周期约60ms,扫描频率约16Hz,能够准确检测出的脉冲频率应低于8Hz,当转速的脉冲频率大于16Hz,即转速n≥480r/min时,PLC受其扫描频率的影响,不能准确检测出脉冲的个数,情况不好时,会出现高速时检测的脉冲个数很少,误判为电动机基本停止而进行下面动作,造成事故。此种方案只适用于主轴低速旋转状态的监测。
第二种方案:检测脉冲信号持续为“0”或“1”的时间T,当n<60r/min时,发出主轴停止完了信号。由于PLC程序执行过程的延时,数控系统收到主轴停止信号,并执行下面动作时,主轴已完全停止旋转,n=60r/min所对应脉冲信号持续为“0”或“1”的时间T为0.25s,因此我们把检测脉冲信号的计时器设定为0.25s。同样高速时也会出现脉冲测不准的情况,但不管情况多坏,在0.25s的时间内“0”或“1”至少变化一次,因此可以准确地判断主轴是否停止旋转。此方案可以适用于主轴高速或低速旋转时主轴制动状态的检测。在实际应用中,我们采用了此方案。
PLC实现主轴能耗制动的控制方法
PLC设计程序中,X20.0为转速脉冲信号的输入,M05为主轴停止信号,Y50.0为主轴停止完了信号。
两个计时器TM1、TM2分别判断X20.0脉冲信号持续为“0”或“1”的时间是否达到设定的时间,只要有一个时间到达,即R100.1或R100.2变“1”,导致R100.3变“1”,此时M05为“1”,导致Y50.0输出“1”,则发出主轴制动完了信号,实现了主轴停止的准确判断。
上一个:高速电机如何拆卸
返 回